Introduction of Recessed Plate filter press
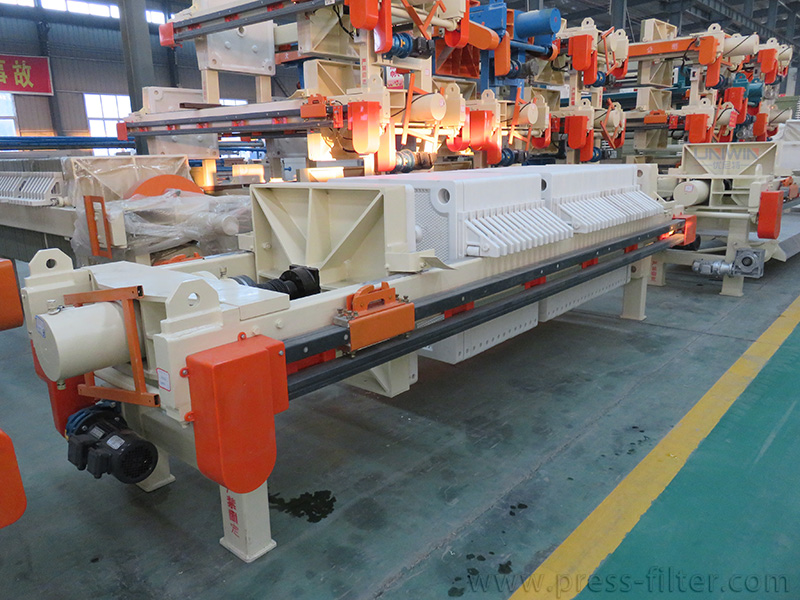
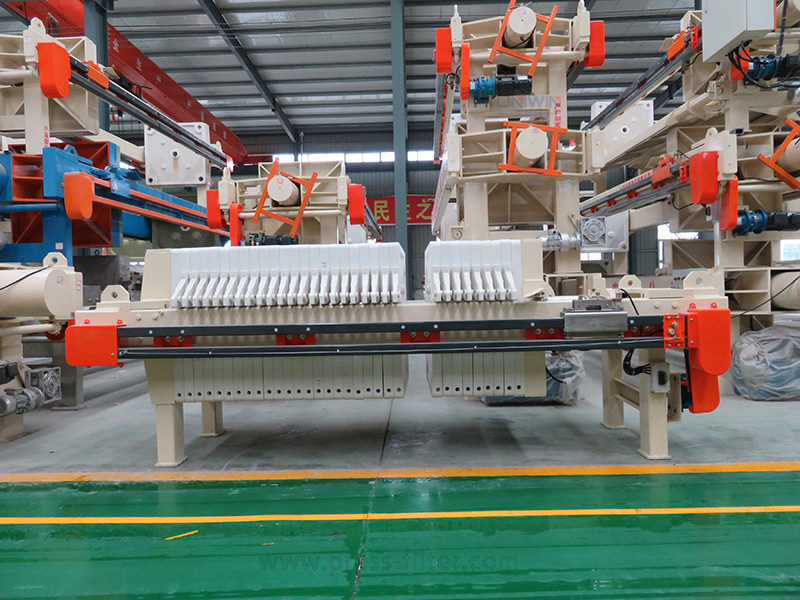
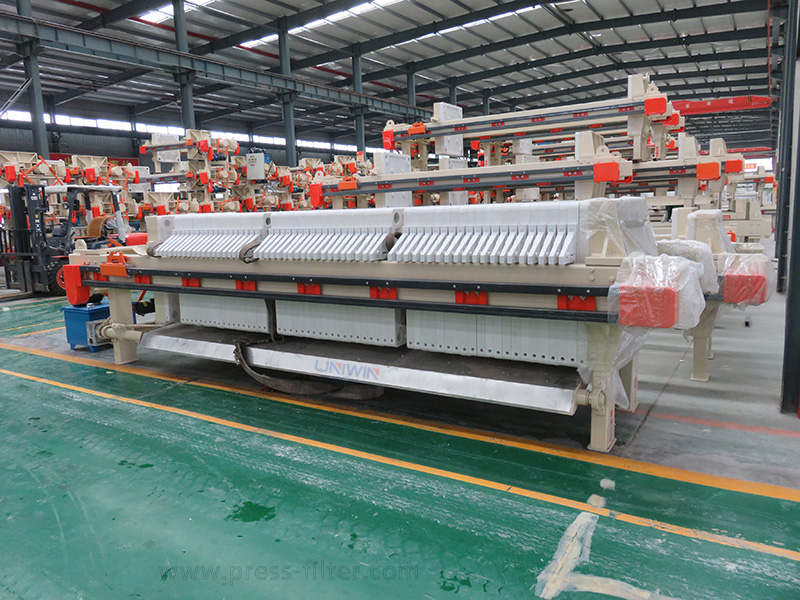
Recessed Plate filter press Working Principle:
- The material is pumped into the filter press through the feed, and the solids are evenly distributed in the filter chamber. The solids start to accumulate on the filter cloth, and eventually, the solids start to form a filter cake on the filter press cloth.
- Filtrate typically exits the filter plates through corner ports and enters the manifold. When the correct valve in the manifold is open, the filtrate leaves the filter press through the outlet.
- As the filter presses build up pressure, solids accumulate in the filter chamber until the filter cake is completely filled. The filling cycle is completed when the filter chamber is full of filter cake. Then, the press is turned on, the filter press plate is moved, and the filter cake falls into the filter cake hopper.
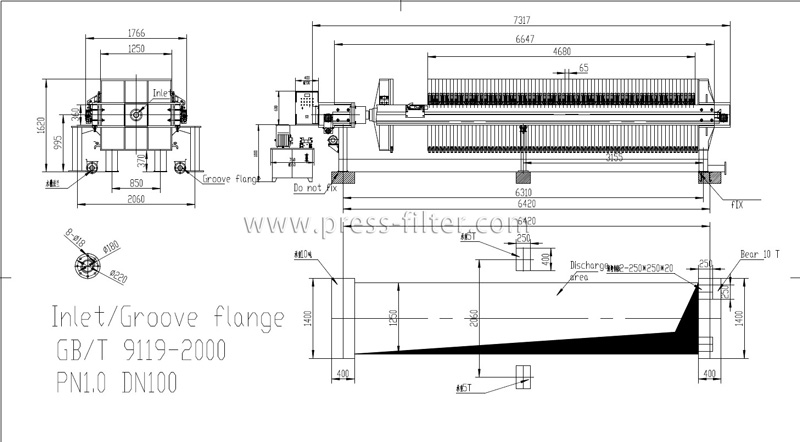
Difference between plate and frame filter press and recessed chamber filter press
- Feeding position: The common feeding method of the chamber filter press is middle feeding, and some old equipment is middle-upper feeding or corner feeding; the feeding of the plate and frame filter press is corner feeding.
- Filter press plate structure: The filter plate of the recessed plate filter press is an integral filter plate. The plate and frame filter plates are a combination of two parts: a plate and a frame.
- Degree of automation: The chamber filter press can realize automatic operation, but the plate and frame filter press cannot realize automatic operation.
Filter plate of the Recessed Plate filter press
Filter Cakes
Parameter
Model | Filter area(m2) | Plate size (mm) | Cake thickness (mm) | Filter chamber volume(L) | Plate Number (pcs) | Filtration pressure (Mpa) | Motor power (KW) | Weight (KG) | Dimensions (L*W*H) (mm) |
---|---|---|---|---|---|---|---|---|---|
XMY4/450-30U | 4 | 500*500 | 30 | 60 | 9 | ≤0.6 | 2.2 | 860 | 1950*700*900 |
XMY6/450-30U | 6 | 91 | 14 | 910 | 2200*700*900 | ||||
XMY8/450-30U | 8 | 121 | 19 | 960 | 2450*700*900 | ||||
XMY15/630-30U | 15 | 700*700 | 226 | 18 | 1725 | 2640*900*1100 | |||
XMY20/630-30U | 20 | 297 | 24 | 1993 | 2940*900*1100 | ||||
XMY30/630-30U | 30 | 452 | 37 | 2360 | 3590*900*1100 | ||||
XMY40/630-30U | 40 | 595 | 49 | 2788 | 4300*900*1100 | ||||
XMY30/870-30U | 30 | 870*870 | 460 | 23 | 2580 | 3330*1400*1300 | |||
XMY50/870-30U | 50 | 748 | 38 | 3318 | 4260*1400*1300 | ||||
XMY60/870-30U | 60 | 902 | 46 | 3712 | 4700*1400*1300 | ||||
XMY80/870-30U | 80 | 1210 | 62 | 4561 | 5580*1400*1300 | ||||
XMY80/1000-30U | 80 | 1193 | 46 | 5259 | 5120*1500*1400 | ||||
XMY100/1000-30U | 100 | 1473 | 57 | 5985 | 5800*1500*1400 | ||||
XMY120/1000-30U | 120 | 1777 | 69 | 6776 | 6500*1500*1400 | ||||
XMY100/1250-30U | 100 | 1250*1250 | 1468 | 36 | 6728 | 5020*1770*1600 | |||
XMY160/1250-30U | 160 | 2341 | 58 | 8205 | 6450*1770*1600 | ||||
XMY200/1250-30U | 200 | 2896 | 72 | 10851 | 7360*1770*1600 | ||||
XMY250/1250-30U | 250 | 3650 | 91 | 12834 | 8600*1770*1600 | ||||
XMY300/1500-30U | 300 | 1500*1500 | 5235 | 74 | 25526 | 8130*2200*1900 | |||
XMY400/1500-30U | 400 | 6985 | 99 | 32074 | 9880*2200*1900 | ||||
XMY500/1500-30U | 500 | 8735 | 123 | 38106 | 11560*2200*1900 |
Applications
- Chemical industry
- Metallurgical industry
- Coal industry
- Petroleum industry
- Food industry
- Pharmaceutical industry
- Printing and dyeing industry
Customer Visiting
Advantages
- Feed through the center hole, allowing the filter chamber to fill faster and more evenly, reducing the risk of filter plate damage due to uneven pressure.
- Higher feed pressure can be achieved by alcove design, which can prevent the filter plates from bending under high pressure.
- Cake release is easier with concave plates. When using a plate and frame filter press, the filter cake may not be released as quickly and may require more operations to remove.
- The machine adopts mechanical, electrical, and hydraulic integrated design and manufacture, with reasonable structure, simple and reliable operation, and convenient maintenance.
Packging&Shipping
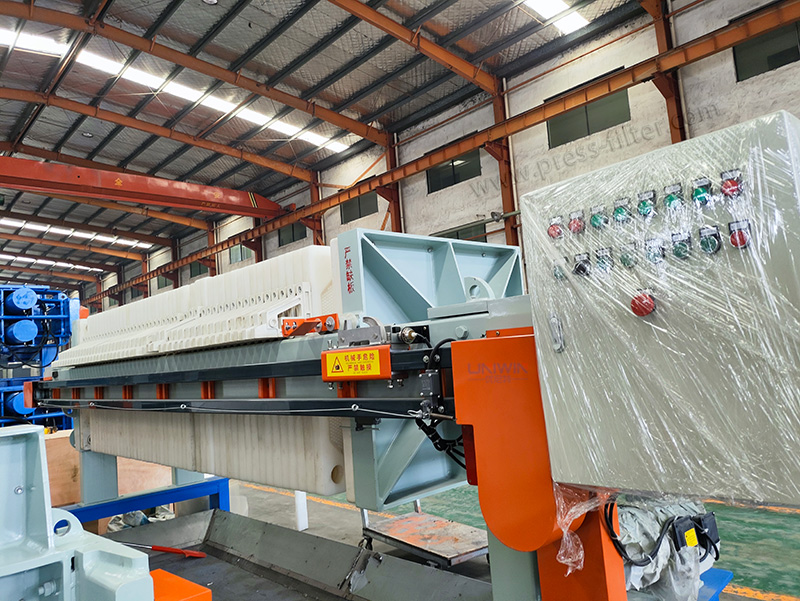
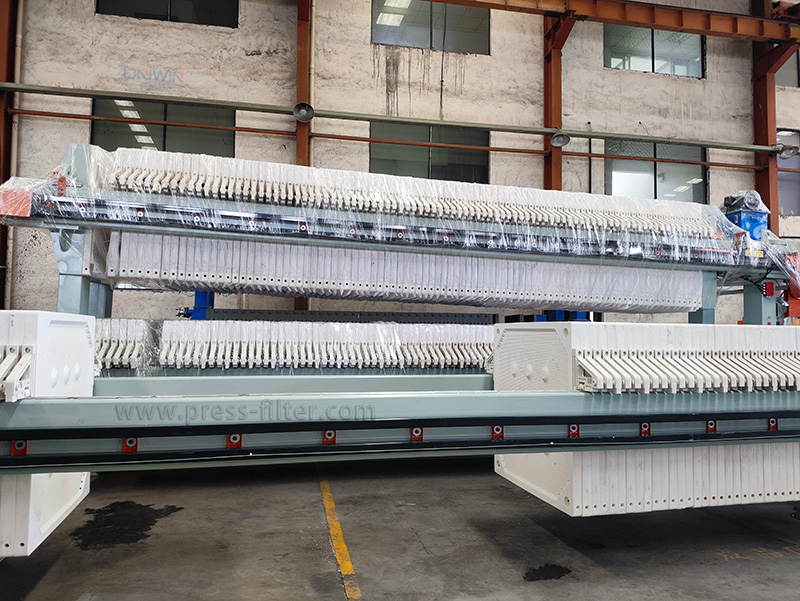
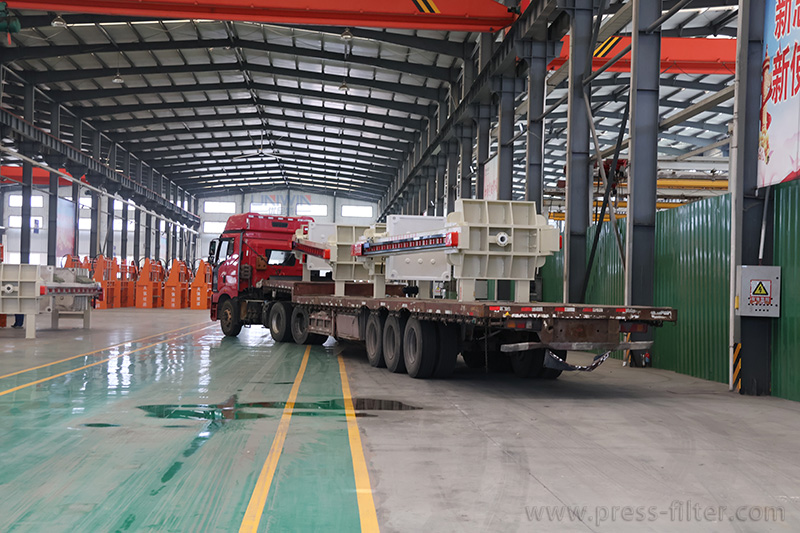
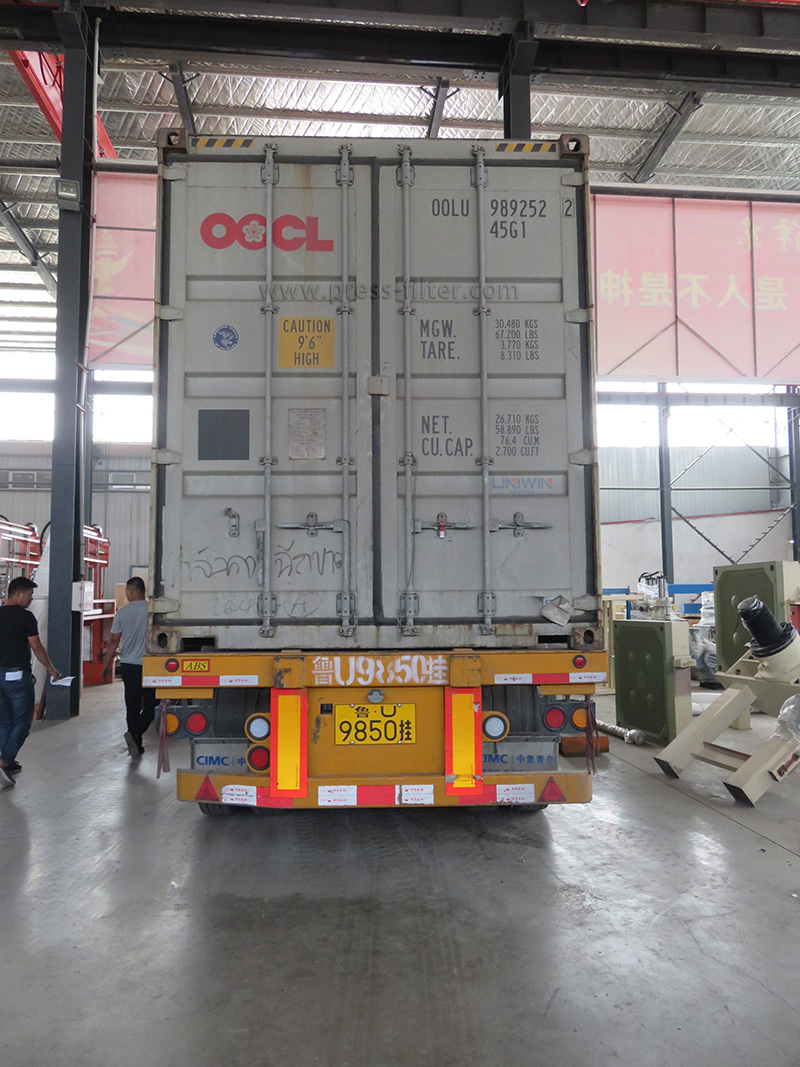
Precautions for the operation of press filter
1. Select filter cloth correctly. Clean the filter cloth regularly and promptly to keep the surface of the filter press clothes clean and free of residues. If the filter cloth becomes hard, it should be softened. If the filter cloth is damaged, it needs to be replaced with a new one in time.
2. Pay attention to protecting the sealing surface of the filter plate to avoid deformation of the filter plate due to collision.
3. The temperature of the material to be filtered should be ≤100°C and the liquid must not be mixed with debris or hard objects that damage the filter plate.
4 Valves for materials and washing water must be opened and closed according to operating procedures, and materials and washing water must not enter at the same time.
5. Keep the machine clean, keep the workplace hygienic, and keep the roads clear.
6. After the work is completed, turn off the power, organize the tools, clean the remaining materials in each part of the machine, and do a good job in equipment maintenance and cleaning of the work site.